Here is the rewritten content with the same meaning, length, and proper headings:
Imagine being the quality control manager at a prominent electronics manufacturer, where a recurring component issue with a newly released product has led to a recall. Historically, the only solution would be a full recall, resulting in significant financial, operational, and reputational consequences. However, with the implementation of a digital thread framework as part of an industrial transformation strategy, your organization can now provide comprehensive visibility into its data. In just a few clicks, you can trace the entire production history of the defective product, from design to final assembly, and identify a fault in a specific batch of components sourced from a single supplier. This enables you to determine the exact scope of the affected products, work with the supplier to resolve the issue, and initiate a targeted recall, thereby minimizing customer inconvenience and preserving the company’s brand reputation.
Over the past decade, the concept of a digital thread has been the holy grail of data touchpoints, providing a real-time view of a product’s entire lifecycle, from design to end-of-life. However, this has remained largely out of reach for most industrial companies due to two primary reasons:
- The data problem: Fragmented, siloed, and uncontextualized data across a heterogeneous stack of technologies and modalities, requiring significant investments in data science techniques to leverage for specific use cases, with limited scalability.
- Return on investment (ROI): Traditionally, it has been challenging to prove ROI for digital thread initiatives, partly due to the data problem and partly due to the complexity of acting on insights, including cultural resistance, skills gaps, and other factors.
Microsoft, in collaboration with partners like PTC, believes that digital threads are becoming an attainable reality for industrial customers due to two key innovations. Firstly, the rise of unified data foundations that make data usable by securely sourcing it from systems like CRM, PLM, ERP, and MES, and automating contextualization aligned to any given standard or custom data model. Secondly, the emergence of generative AI, specifically AI agents that reason using this unified data foundation and provide insights or take actions, unlocking thousands of use cases across the manufacturing value chain.
The role of AI agents
AI agents are sophisticated software systems designed to automate complex analyses, support decision-making, and manage various processes. They are productivity enablers that can effectively incorporate humans in the loop through multi-modality. These agents are designed to pursue complex goals with a high level of autonomy and predictability, taking goal-directed actions with minimal human oversight, making contextual decisions, and dynamically adjusting plans based on changing conditions. AI agents can assist in various business processes, such as optimizing workflows, retrieving information, and automating repetitive tasks.
A leading example of a domain-specific agent is PTC’s Codebeamer Copilot, which supports software development processes for complex physical products, like software-defined vehicles. Codebeamer Copilot leverages the Codebeamer data graph for a connected and comprehensive view into the product development process, providing rapid insights into key areas of application lifecycle management (ALM). The result is automated requirements handling, enhanced quality control, and boosted productivity due to drastically reducing the time it takes for engineers to write and validate requirements.
The AI-powered digital thread provides agents with the combined knowledge of the entire manufacturing data estate, with multiple domains, removing their previous limitations of being confined to one function.
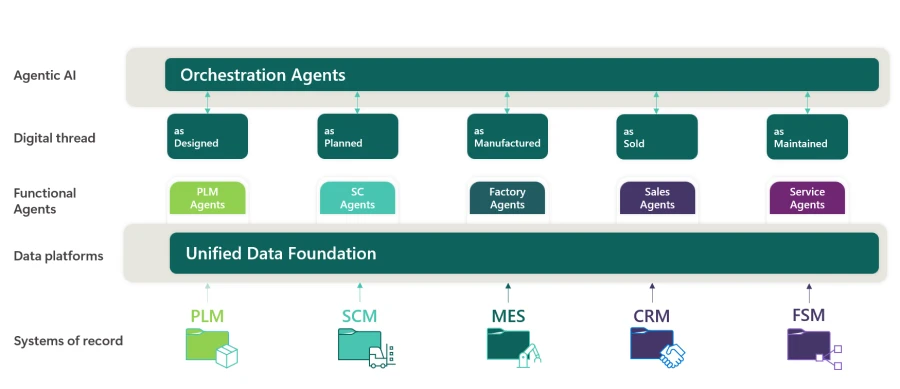
Real-world applications of AI-powered digital threads
The era of AI and digital threads has arrived, and it’s delivering real value for the world’s leading manufacturers today.
Schaeffler
Schaeffler, a manufacturer of precision mobility components, faced a need to modernize data management, as its data previously took days to decode. Their goal was clear: find a scalable solution to uncover factory insights faster. An agent was implemented to allow frontline workers to immediately uncover detailed information when faced with unexpected downtime, enabling them to get the line running again faster and reducing costly delays in production.
Bridgestone
Bridgestone, the world’s largest tire and rubber company, leverages manufacturing data solutions in Microsoft Fabric to accelerate the productivity of their frontline workforce. As a private preview customer, in collaboration with a Microsoft partner, the company uses digital thread and AI technology to address key production challenges, like yield loss. The query system solution enables frontline workers, with various levels of experience, to easily interact with their factory data and efficiently uncover insights to improve yield and enhance quality.
Toyota O-Beya
Toyota is leveraging AI agents to harness the collective wisdom of its engineers and accelerate innovation. At its headquarters in Toyota City, the company has developed a system named “O-Beya,” which means “big room” in Japanese. This system consists of generative AI agents that store and share internal expertise, enabling the rapid development of new vehicle models. The O-Beya system currently includes nine AI agents, such as the Vibration Agent and Fuel Consumption Agent, which collaborate to provide comprehensive answers to engineering queries.
The road ahead
The journey to fully realizing the potential of AI-powered digital threads involves phased implementation. Starting with identifying the right use cases aligned to business goals, where AI agents can play a role. Secondly, identifying if the right data is available and in the right standards for usability. Lastly, quickly proving value by implementing a set of initial use cases with a minimum viable digital thread and measuring and socializing its results.
- Azure adaptive cloud approach to source data from the edge, while supporting application modernization following cloud patterns.
- Partner applications as systems of records, like PTC Windchill.
- Microsoft Fabric as the unified data platform, and Manufacturing Data Solution in Fabric as the data transformation and enrichment service for manufacturing operations.
- Microsoft first-party manufacturing agents, like Factory Operations Agent in Azure AI Foundry, to unlock high-value factory use cases.
- Microsoft AI platforms like Azure AI Foundry and Microsoft Copilot Studio to support development and orchestration of custom AI agents.
- Partner applications with agentic AI capabilities embedded, for example PTC ServiceMax AI.
Learn more
Microsoft Cloud for Manufacturing
Manufacture a sustainable future
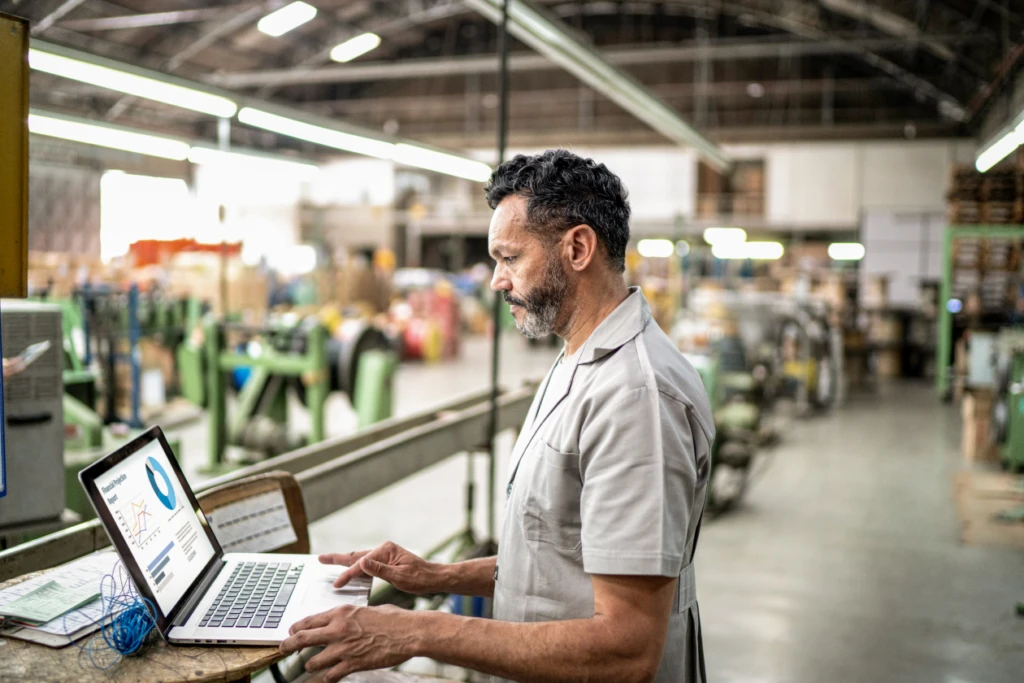
Source Link